CATEGORIES
Regular silo inspections and routine silo maintenance help you increase the useful life of your silo, reduce unplanned downtime, and uphold production goals. In-house examination of the silo exterior is a good start in making sure silo walls are sound, but it should never replace a professional inspection.
Silo walls undergo an enormous amount of stress horizontally and vertically during their normal useful life. This stress can result in cracks or, for stave silos, offset stave joints. Cracks can allow moisture intrusion into the silo and cause additional issues inside. They can also signify delamination, which can compromise steel reinforcement integrity and lead to structural failure.
Determining the severity of exterior wall damages is an easy task for professionals. Yet, there can be limitations due to site hazards or other obstacles that can make visibility a challenge. Artificial intelligence (A.I.) supplemental inspections, offered exclusively by Marietta Silos, remove any guesswork when it comes to exterior silo inspection.
Drone capture technology allows faster, more accurate exterior inspections by obtaining images and videos of the entire silo or bulk storage container exterior. These images are then run through A.I. algorithms that can detect even small defects (smaller than 0.1 mm) and map the precise location onto the captured silo image for future examination.
Learn more about Artificial Intelligence, 3D Damage Tracking Silo Inspection in our video or view our full library of videos on silo inspection, silo maintenance, and silo restoration on 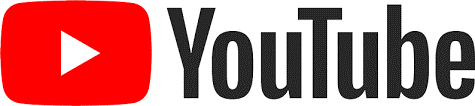
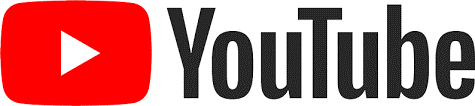
Silos are unique structures, and waterproofing coatings are not created equal. Silo coatings like floating membranes and roofing tar are some of the cheapest to acquire. However, they are also the most likely to fail during the normal use of a metal or concrete silo. Membranes are easily punctured during routine loading and unloading or even through heavy foot traffic. Roofing tar, on the other hand, cannot tolerate foot traffic. Tar also naturally softens by the sun, allowing stored material to stick into the surface and create buildup that is extremely difficult to remove. In cold weather, tar solidifies and can easily crack and allow moisture to penetrate the silo and jeopardize stored material. Sprayed polyurethane coatings similarly do not tolerate foot traffic, are easily punctured and are sensitive to humidity.
The most effective, monolithic barrier against moisture is a rubberized coating that bonds directly to various surfaces to repair cracks and seal penetrations, laps and fasteners. Rubberized coatings have a high elasticity coefficient that moves with silo vibration caused by roof-mounted equipment or loading and unloading.
Our rubber coating reduces costly reapplications of surface protectants and can be applied to many surfaces. As a silo roof coating, our rubber coating can fix both metal silo roofs and concrete silo roofs. In addition, our silo roof-top coating has the flexibility to maintain its integrity through the changing seasons, protect against oxidation, humidity and corrosive environments while resisting alkali, salts, abrasions and fumes.
Rubber Roof-Top Coating Works On:
- Metal buildings and roofs
- Built-up roof (BUR) membranes
- Grain silos and bins
- Silo exterior walls
- Single-ply roofs
- Urethane foam roofs
- Steel bolted joints
- Concrete silo roofs
Additional Benefits of Rubberized Silo Coatings:
- Not a floating membrane
- Offers excellent adhesion to aluminum, galvanized steel, painted surfaces, modified bitumen, steel joints and many other surfaces
- Excellent in sealing cracks, laps, fasteners and roof surface penetrations
- Available in all 50 states and a variety of colors
Our roof-top silo coating method is a proven industrial roof coating system that keeps elements out and stored materials dry. Request a quote from us today.
Proper material flow in silos is important for more than just production schedules. Issues with material flow can cause increased stress on silo walls that may go beyond what the silo was designed to withstand. Not only does this cause cracking, spalling and possible wall separation, it can also lead to structural failure.
Silos that were initially designed with internal reinforcement sometimes face cracking or delamination of the concrete. When this is seen on the silo exterior, it is important to schedule a silo inspection as soon as possible. Such damages are often caused by overstressing of the horizontal reinforcing as a result of material flow issues.
What is silo post-tensioning?
Tension is a critical component in silo repair. If the silo is still structurally sound, certain damages caused by failing interior steel reinforcement can be repaired by post-tensioning. Post-tensioning silo repair uses high-strength post-tensioning strands that are placed around the exterior of the silo. These tensioned bands essential take over the structural support of the original internal steel by keeping walls sturdy against additional stress caused by asymmetric flow.
During this restoration process, a qualified engineer uses factors such as silo size, stored material weight and how the silo is used to determine tension specifications necessary specifications for wall reinforcement. After the strands are properly tensioned through a hydraulic process, steel lock couplers are positioned and tightened. Once completed, the tensioning assures that the silo can be safely used. Once the silo is restored through post-tensioning, it can then be returned to its actual load capacity.
Request a silo repair quote by scheduling your inspection today.
View our video, How Often Should I Have My Silo Inspected, or view our full library of videos on silo inspection, silo maintenance, and silo restoration on 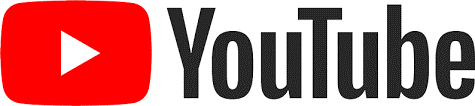
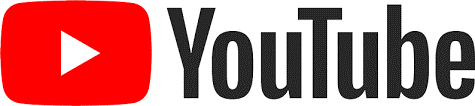